SEMICONDUCTOR FABRICATION
FTMC operates a III-V group elements semiconductor foundry. A complete solution for Research and Development. We have:
Implemented ISO 9001 quality standards;
ISO5 and ISO7 cleanroom facilities:
Equipment:
Two molecular beam epitaxy reactors for III-V compounds;
Thin film deposition and etching
- Magnetron sputtering system
- E-beam sputtering system
- Double tube PECVD for SiNx, SiO2, Al2O3, SiC, graphene
- Chlorine chemistry ICP RIE system
- Fluorine chemistry RIE system
- PECVD reactor for SiNx, SiO2 coatings
Lithography
- Laser Lithography system with 600nm resolution
- Mask Aligner 0.8um resolution.
Magnetron sputtering Angstrom Engineering EvoVac
The magnetic sputtering device features a 20x20x20 inch chamber equipped with four magnetrons and a Kaufman and Robinson EH400 5A ion gun. One of the magnetrons operates in radio frequency (RF) mode only, another in direct current (DC) mode only, the third can switch between RF and DC, and the fourth is a high-power pulsed magnetron (HiPIMS), capable of reaching up to 1MW peak power per pulse. This magnetron is powered by three sources: a 1.2kW DC Glassman Sputter, an Advanced Energy 5kW Pinnacle Plus DC (HiPIMS), and a 300W RF VII Power Supply. This setup enables the deposition of layers from conductive and insulating materials, magnetic targets, and layers with unique properties requiring a high degree of ionization of the vaporized material.
Before layer deposition, the surface can be cleaned in the same chamber by bombarding it with ions, ensuring process continuity. Ion bombardment can also be used for complete layer removal. The thickness of the deposited layer is controlled either through power-time mode or by using two QCM (Quartz Crystal Microbalance) sensors. A cryogenic pump ensures a vacuum level of no worse than 9*10⁻⁸ Torr. The large sample holder allows vapor deposition on samples up to 12 cm in diameter, and during the process, samples can be heated up to 600°C. The holder’s distance from the target can be adjusted, and its rotation (0-50 rpm) ensures uniform layer deposition across the entire sample. Sample loading is performed via a LoadLock system—a separate vacuum chamber isolated from the main chamber by a pneumatic valve. An advanced gas pressure distribution controller allows control of mixtures of up to three different gases (O2, N2, Ar). Currently available materials include Al, Ni, Cr, Ti, Sn, In, and Cu.
Offered services:
- Surface cleaning/etching through argon or oxygen ion bombardment
- Formation of metallic contacts
- Deposition of thin metal oxide layers
- Formation of alloys from two different materials
E-Beam system VST Model TFDS–870
The E-Beam evaporation system consists of a glove box and a deposition chamber. First, samples are introduced into the glove box, which is filled with nitrogen gas. The deposition chamber is designed for coating samples with thin layers of various materials and for evaporating contacts.
The chamber maintains a vacuum level of 8×10⁻⁸ Torr. Available sources include gold (Au), a gold-germanium alloy (AuGe12%), germanium (Ge), nickel (Ni), titanium (Ti), and aluminum (Al). The maximum sample size is up to 2 inches in diameter. The sample holders come with four clamps each, allowing up to four smaller samples to be processed at once, provided the total area does not exceed 2 inches in diameter.
The system also has the capability to heat the trays up to 150°C. The sample holder can rotate (0-28 rpm), ensuring uniform coating of the sample. The rate and thickness of the thin film deposition are measured with a Telemark controller (Model 880), which performs ten measurements per second with a thickness accuracy of ±0.5%, plus one least significant digit. The sensor crystal operates at a frequency of 6 MHz (range: 5 MHz to 6 MHz). The typical deposition rate is 2 Å/s.
The use of samples containing zinc (Zn) is strictly prohibited!
Laser Maskless Lithography System Heidelberg Instruments DWL 66+
- 350 mW continuous laser;
- 405 nm wavelength;
- Working area of 200×200 mm;
- Maximum resolution of 600 nm (writing speed: 6 mm²/min);
- 2 μm resolution – 140 mm²/min;
- Supports both raster and vector modes (vector mode resolution >2 μm);
- Minimum sample size: 1×1 cm²;
- Double-sided alignment (only for 10×10 cm² samples).
ISO7 and ISO5 clean room facilities
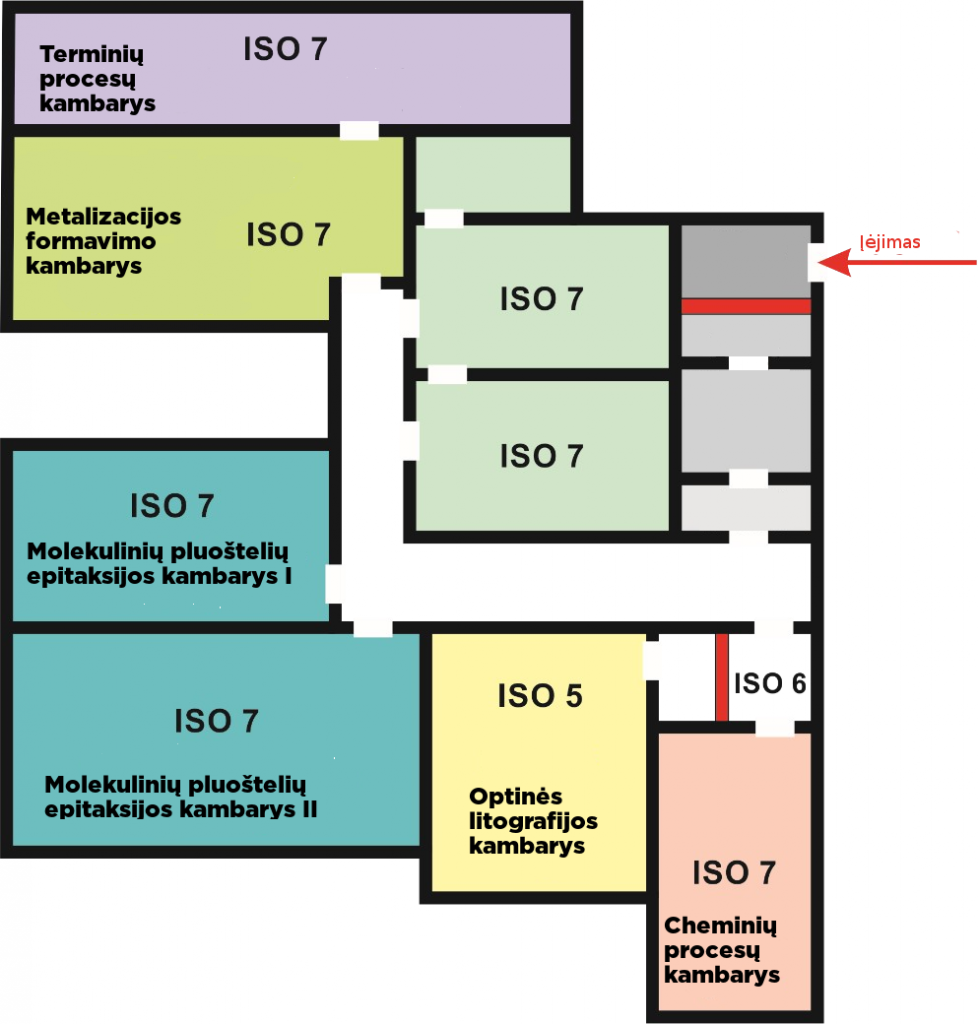