DIRECT METAL LASER SINTERING
DESCRIPTION, INNOVATION AND ADVANTAGES
Direct Metal Laser Sintering (DMLS) is an additive manufacturing technology that is commercially used for metal part fabrication. This technology allows to manufacture of high accuracy strong and durable components of complex geometry and can be used for the fabrication of three-dimensional cooling channels, moulds or topologically optimised parts. Part fabrication, investigation of DMLS process and novel material testing are done applying the EOSINT M280 machine. The EOS EOSINT M280 is an industrial 3D printer based on DMLS 3D printing technology. This 3D printing technique uses a fibre laser to melt and fuse fine metal powder. The printer has a 200 W built-in Yb (Ytterbium) fibre laser with a wavelength of 1060-1100 nm. The maximum build size is 250x250x325 mm3. Different metal powders such as stainless steel, aluminium, cobalt-chromium or titanium can be used in the printing process using a layer thickness of 20 or 40 µm.
CURRENT STAGE OF DEVELOPMENT
Ready for work.
INTELLECTUAL PROPERTIES RIGHTS STATUS
In–house know-how.
TYPE AND ROLE OF PARTNER SOUGHT
Space, aviation, automotive, medicine companies.
Value proposition
This additive manufacturing technology enables the production of high-precision, robust, and durable components with complex geometries. It’s ideal for creating three-dimensional cooling channels, moulds, or topologically optimised parts using a variety of metal powders.
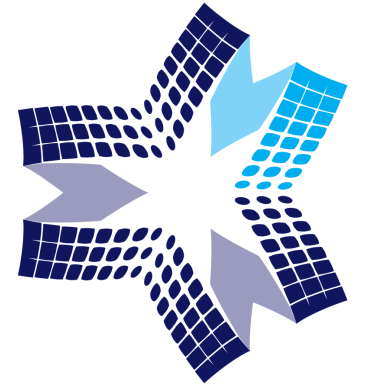